Electronic Design Reviews
A design review is a thorough evaluation of a product, with reliability and compliance being the main focus. Conducting a design review during the initial stages of product development is highly beneficial as it ensures that the product is fully functional before the final stages. This enables businesses to save resources, reduce costs, and, most importantly, speed up their time to market.
To achieve these goals, it is essential to have a design review methodology in place. This ensures the product is functioning as planned throughout all stages of development.
Therefore, the design review should take place as early as possible in the design stage to avoid any need for redesign, retooling, or rework later in the process.
How Does a Design Review Work?
The main objective of a design review is to anticipate potential risks and failures of a specific product or component. To start a typical design review, you need to gather as much information as possible about the product in question. This includes identifying the end-user of the product, the conditions the product will be exposed to, its expected performance, its desired lifespan, and more. This information will guide and facilitate your design review process and clarify the conditions that the product will likely encounter throughout its lifecycle.
The design review process typically follows a series of eight steps:
- Establish a reliability goal
- Quantify the use environment
- Circuit analysis
- Bill of Material (BOM) component stress review
- Printed circuit board (PCB) analysis
- Design for manufacturability (DfM)
- Reliability test plan development
- Failure analysis
After completing these steps, you should have an analysis of the conditions that caused any (or potential) failures, along with potential solutions such as revised parts placement and new material selections.
The Design Review Process
The product design reliability is ensured through a nine-step design review process. Let’s explore each step in detail.
Establishing a Reliability Goal
It is important to establish a product reliability goal that is comprehensive and specific to your objectives. This includes identifying the desired life expectancy of the product, its operating functions, and its performance. Simply stating that the product’s reliability goal is to be “better than last year’s product” or to have a “5-year lifespan” is not enough. Reliability goals should be detailed and robust, taking into account factors such as past products’ field performance, market positioning, cost of failures, technical capabilities, and more.
Best practices for setting reliability goals include basing them on survivability, with confidence levels such as 95% reliability with a 90% confidence level over a period of 15 years. It is also important to avoid using mean time to failure (MTTF) and mean time between failures (MTBF), as these do not accurately measure reliability. MTBF has often been calculated using empirical prediction handbooks, which assume a constant failure rate that is not always correct.
To gain a deeper understanding of how a product’s desired lifetime and environment affect its design, it is recommended to employ physics of failure (PoF). While this requires substantial effort, the return on investment is valuable.
Quantify the Use Environment
Designing a reliable product involves examining all possible use scenarios and environmental stressors, including thermal and mechanical conditions, such as temperature, humidity, shock, vibration, drops, mechanical bending, and product storage and housing. Quantifying these potential scenarios and use environments is crucial to develop a reliable product and effectively evaluate a product design.
Circuit Analysis
Customers often request a thorough evaluation of their schematic as part of the design review. At Ignys, we begin by reviewing the product specifications to fully comprehend the requirements and environments. We ask important questions like: Is the operating temperature range sufficient? Are the standards and levels appropriate and high enough? Are there environments involving shock and vibration?
A circuit analysis is then conducted to ensure that the circuit will function as intended. Electromagnetic capability (EMC) and electrostatic discharge (ESD) risks are identified, and the derating of the components is verified by assessing power dissipation, voltage ratings, dV/dt ratings for field-effect transistors (FETs), Vgs breakdown of FETs, and the temperature rating of the parts.
BOM (Component) Stress Review
To ensure that an assembly is reliable and performs well, it is important to understand how individual components behave under stress. You need to know if all components on the board are compatible and if there are any components that can be eliminated right from the start. This is where a component stress review comes in handy as it helps to streamline the design review process.
The first step in this process is to examine the datasheets for every component that makes up your assembly. This will enable you to:
- Determine the operating temperature range of each component to identify the parts that have the least amount of margin with respect to the operating conditions.
- Identify a replacement part with better margins.
- Analyze the materials used in your components’ manufacturing, as different materials have different compatibilities within the circuit board.
- Examine critical components such as optoelectronics, custom parts, memory devices, electro-mechanical components, and ceramic MLCC capacitors to ensure that the expected product life is met.
- Evaluate new technology devices to determine if the new, finer geometries will function for the intended duration of operation.
All components in the Bill of Materials (BOM) are examined for derating criteria, moisture sensitivity level (MSL), and temperature sensitivity level (TSL). This analysis often identifies parts where extreme care must be taken during manufacturing to ensure that no moisture penetration occurs. A tin whisker analysis may also be performed to assess the susceptibility of the component leads and the surface finish of the printed wiring board (PWB) to whiskering. Whiskering occurs due to the presence of a compressive stress gradient within the tin deposit, which drives the preferential diffusion of tin atoms.
Electrostatic discharge (ESD) susceptibility must also be examined. It is recommended that the user knows the ESD rating for each part and selects parts that achieve the best ESD rating where possible. The designer should identify all ESD-sensitive parts on drawings and mark the locations of ESD-sensitive parts on the board with the ESD symbol. Finally, the user must be aware that part location, particularly with respect to I/O signals, drives the appropriate ESD rating.
PCB Analysis
As electronic components become faster and more complex, it has become increasingly important to conduct a detailed analysis of the Printed Circuit Board (PCB) during the design process. Leaving the critical PCB stack-up design to chance is no longer a recommended practice.
- Cost sensitivity
- Volume of product (finish availability)
- Tin lead solder (SnPb) or load finish (LF) processes
- Shock/drop concerns
- Cosmetics concerns
- User environment (corrosion concerns)
- Fine pitch assembly (<0.5 mm)
- Wave solder required (PCB > 0.062”)
- High yield in-circuit test (ICT)
Design for Manufacturability (DfM)
Design engineers must consider the manufacturer’s abilities and limitations when striving for optimal reliability. While engineers can simulate, test, and design the perfect product, if the manufacturer cannot produce the completed design or procure optimal materials, the designed product may fall short of reliability expectations or may not even be possible to construct.
The DfM review involves assessing the pad geometries used in the layout to determine long-term reliability. The potential for shadowing during the reflow operation or conformal coating is ascertained during component placement. This action involves analysing the proximity of parts to PCB edges, press-fit connectors, and the potential effects of improper ICT fixturing.
Measurement of trace separation ensures that the voltage levels applied comply with IPC-2221. Cleanliness and contamination are examined by looking at the fluxes, handling procedures, and any other potential sources of contamination.
Finally, the DfM analysis examines the manufacturing flow by asking several questions:
- Does the board use single- or double-sided surface mount technology (SMT)?
- Are through-hole parts used?
- Are they wave or selectively soldered?
- Are any parts hand-soldered?
- Are we employing no-clean processing?
- Does the assembly require conformal coating?
- What type of coating?
- How does it compare to different thermal environments?
Reliability Test Plan Development
Stress testing is a process that evaluates the ability of a product to maintain a certain level of functionality under unfavourable conditions. These conditions may include extreme temperatures or other environmental and physical stressors. Stress tests involve techniques such as highly accelerated life testing (HALT), highly accelerated stress screen (HASS), mechanical shock, vibration, etc. These tests help identify weaknesses in a product’s design much faster than in the field.
When using stress tests to determine operating margins, measurements are taken of the operating temperatures (or other specified stress risks), which are then compared to the ratings of the individual components. If individual components are operating too close to their upper limits, then various parts will be tested at different capacities to determine which part can sustain enough margin to prevent early failure.
Stress tests are essential because they can be initiated relatively quickly to evaluate the life expectancy (temperature cycling) and performance under humidity (temperature-humidity-bias) by using a stress level with an acceleration factor that can be translated to the use environment. For instance, 168 hours (1 week) of thermal cycling may translate to three years in a field environment. If you can successfully complete the 168 hours, you can report that your product will also meet the three-year life expectancy.
In addition to thermal cycling, other tests, such as mechanical shock, vibration, salt fog, humidity testing, etc. may also be involved in developing the test plan portion of the review.
Perform Failure Analysis on Test Failures and Field Returns to Initiate Feedback Loop
When conducting failure analysis, it is crucial to not limit the examination solely to assemblies that failed during preliminary tests. If this were the case, the analysis would only determine what does not work before the product is even introduced to the market, whereas the goal is to establish the reliability of a product in its intended environment of use. Failure analysis should consist of scrutinizing both test failures and field returns (if available) to gain an accurate understanding of field environments and thoroughly identify use cases that may not have been considered in the initial reliability qualifications.
During a design review, failure history can often provide valuable insights into the root cause of failure. For instance, if failures occur rapidly in the field, the root cause may be associated with a manufacturing-related issue. Similarly, if dendritic failures are encountered, they may be a result of cleaning or handling problems in manufacturing or environmental exposure.
Failures that arise during testing protocols must be analysed to ascertain the root cause and take appropriate action. For instance, during HALT testing, failures are identified fixed, and the test is resumed. This helps determine the design’s margins with respect to the test parameters.
Are you considering a design review?
There’s nothing we love more than taking a deep dive into a new product and it’s design. As engineers, we’re natural born problem solvers, so feel free to contact us by using this link for a no-obligation, non-salesy chat. We’re always available, happy to chat shop and would like to learn more about you.
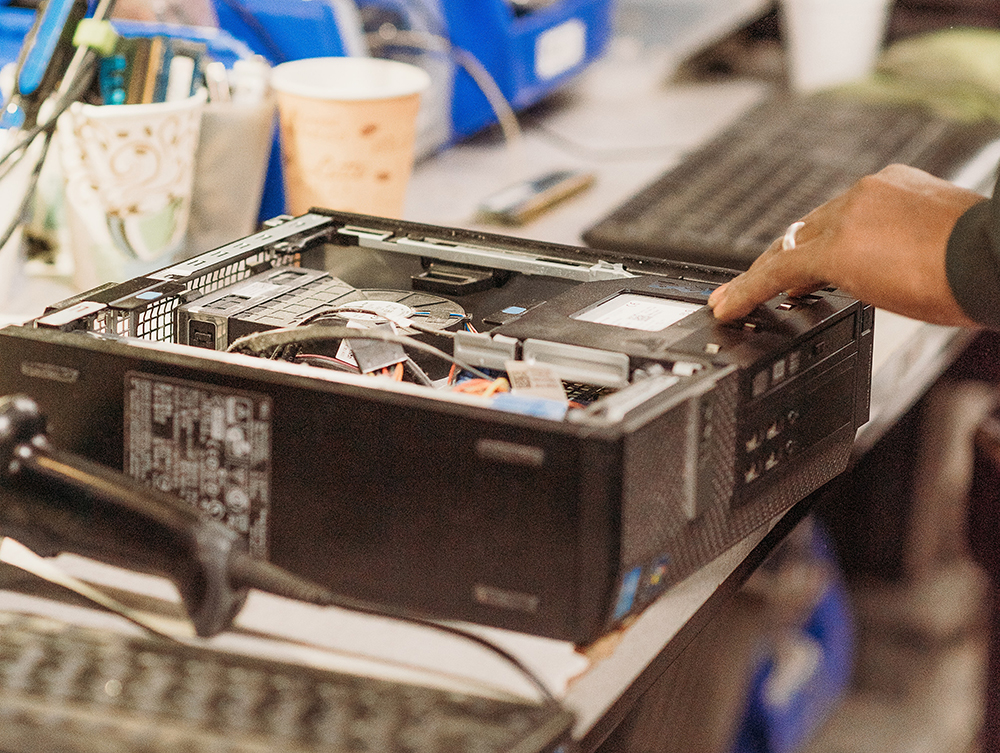